Mechanical seals and their uses in pumps
Key Benefits of Mechanical Seals and Their Uses in Pumps
Mechanical seals are vital components in pump systems. They stop leakage and help pumps to work properly. They can handle high pressures and temperatures. So, they are dependable for oil and gas, chemical processing, and wastewater treatment.
These seals form a barrier between the rotational shaft and stationary parts of the pump. This stops fluid from entering or leaving the system, which means better efficiency and less maintenance.
Mechanical seals come in various designs and materials to fit any job. They can handle different pressures, speeds, and temperatures. Plus, they can help to save energy in pumps. An article by Pumps & Systems magazine explains that mechanical seals can decrease power consumption and lower costs.
In conclusion, mechanical seals are an impressive and necessary part of the pump world.
Understanding the Function of Mechanical Seals in Pump Operations
To understand the function of mechanical seals in pump operations, dive into the basics of mechanical seals and their components. Explore the importance of proper seal selection for pump efficiency. Discover the common challenges faced by mechanical seals and find effective solutions.Basics of Mechanical Seals and their Components
Mechanical seals are essential for pump operations. They're made up of several components, forming a barrier between the pumped fluid and the external environment. This prevents leakage and contamination.
One part is the stationary seat or housing. It stays fixed and provides a stable surface against which the rotating seal face presses. This creates a tight seal. The rotating seal face moves with the pump shaft, keeping contact with the stationary seat.
The secondary sealing element, often an elastomer or O-ring, helps stop any potential leakage. It's flexible and resilient, adapting to pressure and temperature changes without losing its sealing function.
The metal bellows or spring is the last component. It's an axial spring, pushing the rotating seal face against the stationary seat. It compensates for wear and changes in operating conditions, providing enough force for effective sealing.
Pro Tip: Regular inspections and maintenance of mechanical seals can increase their lifespan and improve pump performance. Don't let the wrong seal make your head spin - and your energy bills skyrocket!
Importance of Proper Seal Selection for Pump Efficiency
The proper selection of seals is essential for pumping efficiency. A good seal creates a secure, leak-free connection between the rotating shaft and the stationary pump casing. This reduces friction, saving energy and extending the pump's lifespan.
Factors to consider are the application requirements: temperature, pressure, fluid compatibility. Plus the type of pump and its operating conditions. Picking a seal that fits these specifications will guarantee optimal performance and no downtime.
The sealing technology is also key. Different seals differ in reliability, installation and maintenance needs. Some self-align or require minimal axial space - perfect for tight spaces.
Tip: Consult professionals to make sure the seal is perfect for your system. They can identify issues and help you pick the right seal.
Common Challenges Faced by Mechanical Seals and Solutions
Mechanical seals are very important for pump operations, but they face certain issues. One is leakage, which can cause inefficiencies and damage. To address it, precise fit between the seal and housing, inspection for wear or damage, and promptly replacing worn-out parts are key.
Heat generation is another challenge. High temps can damage the seal material, leading to early failure. Cooling plans like flush or barrier fluids can help reduce heat and extend the seal's lifespan. Also, materials with good heat resistance and optimizing pump conditions can help.
Abrasive particles in pumped fluids also wear down the sealing faces, leading to seal failures over time. Barrier fluids that lubricate and protect against abrasives can be a solution. Also, monitoring particle levels and filtering systems are essential preventative measures.
Misalignment between pump components is another issue. Poor alignment raises stress on the seal faces and reduces their effectiveness. Precision alignment and frequent checks during installation are necessary to avoid misalignment problems.
It's important to consider chemical compatibility and choosing the right seal for the application. Plus, personnel responsible for maintaining mechanical seals should get regular training for correct handling and troubleshooting.
Pro Tip: Knowing the challenges faced by mechanical seals lets you take proactive solutions, reducing downtime and improving pump performance.
Different Types of Mechanical Seals Used in Pump Systems
To ensure efficient pump systems, understanding the different types of mechanical seals is crucial. In order to address this, we'll explore the solutions offered by three key sub-sections: single spring mechanical seals, balanced and unbalanced mechanical seals, and cartridge mechanical seals. Each of these options plays a vital role in maintaining the integrity and reliability of pump systems.Single Spring Mechanical Seals
Single spring mechanical seals are an easy-to-maintain device used in pumps. They use a single spring to apply pressure to the seal faces, creating a tight seal. This prevents leakage and allows for the pump system to remain intact.
These seals are simple to install and maintain. A single spring design makes them attractive when quick replacement or repair is needed.
Single spring seals also provide reliable performance. The balanced force of the single spring reduces wear and extends the seal's lifespan. This means less maintenance and lower running costs.
However, single spring mechanical seals may not be suitable for high-pressure or high-speed applications. In these cases, alternative types might be better.
Consider the case of a manufacturing plant that experienced flooding due to a malfunctioning pump. It was found that the single spring seals couldn't withstand the high-pressure environment.
Experts determined that dual cartridge seals would be better suited. The plant made the change and saw great improvements in pump performance and reduced flooding.
Balanced and Unbalanced Mechanical Seals
Balanced and unbalanced mechanical seals are essential for pump systems. Balanced seals feature components like springs and bellows, to maintain equilibrium between inside and outside pressures. This reduces wear and improves efficiency. On the other hand, unbalanced seals are simpler but more prone to leakage. Without pressure balancing, seal faces can be damaged by pressure fluctuations.
For optimal performance and longevity, balanced mechanical seals are a superior choice. They resist varying pressures without compromising effectiveness. Investing in balanced seals minimizes maintenance costs and prevents unexpected downtime.
When it comes to sealing pump systems, don't take a DIY approach! Cartridge mechanical seals provide the best results. Choose wisely and choose balance! Upgrade your pump system today and experience improved performance and increased operational efficiency.
Cartridge Mechanical Seals
Cartridge mechanical seals are the perfect sealing solution for a pump system. Pre-assembled, they can be quickly and easily installed with no complex assembly. This saves time and lowers the risk of errors.
Their pre-assembled nature also guarantees accurate alignment of the seal faces, meaning better sealing efficiency. This reduces leakage and extends the seal's lifespan, saving costs in the long run.
Cartridge mechanical seals can withstand high temperatures and pressures, making them suitable for a wide range of applications. From sewage to oil rigs, they keep pumps running without interruption.
Choose a reliable manufacturer for the best performance. Upgrade to cartridge mechanical seals for improved performance, reduced maintenance costs and peace of mind. Enjoy the reliability and convenience they bring.
Applications and Industries Utilizing Mechanical Seals in Pumps
To ensure efficient functioning of pumps, mechanical seals find critical applications across various industries. Explore how mechanical seals are utilized in pumps for water and wastewater treatment plants, oil and gas industry operations, chemical processing plants, and food and beverage manufacturing. Each sector benefits from the reliability and performance provided by mechanical seals.Water and Wastewater Treatment Plants
Water and wastewater treatment plants rely on mechanical seals to stop leaks and contamination. They provide a barrier between the pump shaft and casing. This stops any fluids from getting out, keeping the pumps efficient and preserving the treatment process.
These seals handle a variety of contaminants: chemicals, solids, and even biological matter. They are versatile and perfect for the job.
It's important for these plants to have high-quality mechanical seals. If not, there can be leaks, contamination, and even shutdowns of processes. Investing in good seals keeps operations running and helps to protect the environment and water quality.
Oil and Gas Industry
The Oil and Gas industry is highly dependent on mechanical seals in pumps. These seals stop leakage of hazardous chemicals, protect equipment from corrosion, and uphold the pressure during pumping.
Mechanical seals are vital for preserving the integrity of pipelines that transport crude oil and natural gas. They guard against leaks that can trigger environmental disasters or safety issues. A reliable barrier between the pump's rotating shaft and stationary housing is created by mechanical seals, guaranteeing optimal performance and minimal downtime.
Also, mechanical seals utilized for pumping oil and gas production are designed to resist extreme conditions, such as high pressures and temperatures. This is crucial, as these environments are both difficult and hazardous. Mechanical seals help to prevent the admission of contaminants, reducing maintenance costs while sustaining smooth operations.
One example where mechanical seals have proven their value is in offshore drilling platforms. These platforms are affected by the harshest weather conditions at sea and operate under immense pressure for oil extraction from deep beneath the ocean floor. Even in these trying conditions, mechanical seals deliver reliability, protecting against leaks and upholding efficient pumping operations.
The utilization of mechanical seals in pumps in the Oil and Gas industry has transformed its operations. It has improved safety, increased overall efficiency, elongated equipment lifespan, and lessened maintenance requirements. As this sector remains to expand, the need for advanced sealing solutions will keep growing as industries embrace technological advancements to satisfy ever-increasing energy demands.
Chemical Processing Plants
Mechanical seals in pumps are essential for chemical processing plants. They provide an effective barrier to prevent leakage and contamination. Plus, they're made from materials resistant to corrosion and chemical attack. Designs often include double or tandem configurations to give extra protection.
Regulations and standards must be followed to guarantee safety. Maintenance and inspections are needed regularly to detect any potential issues.
The Bhopal gas tragedy is a reminder of how important proper sealing is. Mechanical seals ensure safe operation and minimize environmental pollution. So, cheers to the power of mechanical seals in keeping the food and beverage industry rolling!
Food and Beverage Manufacturing
In the food and beverage industry, mechanical seals are vital. They prevent leaks and contamination, which is so important for food safety.
These seals are used in pumps for many applications. Mixing ingredients, transferring liquids, and packaging products - mechanical seals handle all of these. They can stand high temperatures and pressure - making them ideal for food production.
And they're versatile too. Mechanical seals work with different types of fluids. Even liquids with high alkalinity or acidity levels are no problem.
Maintenance and replacement are easy. And that's great news for manufacturers, as any downtime in production can be costly. Quickly replacing worn-out seals lets them keep production flowing.
Plus, mechanical seals provide an added layer of protection against contamination. Customers can be confident that their products are safe and free from foreign substances.
Benefits of Using Mechanical Seals in Pumps
To achieve optimal results in using mechanical seals in pumps, focus on the benefits they provide. Enhance pump efficiency and performance, minimize leakage and environmental impact, and consider cost-effectiveness and maintenance considerations. These sub-sections cover the key solutions you should understand to make the most out of mechanical seals.Improved Pump Efficiency and Performance
Mechanical seals provide many benefits for pumps. They improve efficiency and performance, by preventing leaks. This means no fluid escapes from the pump, resulting in minimal losses. The pump maintains a steady flow rate and pressure, maximizing its effectiveness. Fewer breakdowns and malfunctions, mean less downtime and repair costs. Regular maintenance and inspection will further enhance their longevity and performance, making your pumping operations more efficient.
Seal the deal with mechanical seals - goodbye leaks, hello happy planet!
Reduced Leakage and Environmental Impact
Mechanical seals play an essential role in reducing leakage and protecting the environment from pumps. They are designed to effectively contain fluids, so no leaks or spills occur. These minor leaks can have big environmental impacts if left unchecked. With mechanical seals, this risk is minimized and a secure seal is maintained even under extreme conditions.
Moreover, mechanical seals have unique features that make them more effective at containing fluids. They can withstand high-pressure environments and keep a tight seal, eliminating the possibility of any leaks or spills.
Not only do mechanical seals reduce leakage, but they also help conserve valuable resources by preventing wastage. This is beneficial for industries financially, and also globally, as it promotes responsible resource management.
Using quality mechanical seals is not only beneficial for the environment but also for businesses. Companies that prioritize using these seals show their commitment to environmental stewardship and gain a competitive edge in the eco-conscious market.
Cost-Effectiveness and Maintenance Considerations
Mechanical seals in pumps provide lots of advantages. They are tough, meaning less need for repair or replacing. Plus, they prevent leakage, which makes the pump more efficient and can save on energy bills. Also, they need only minimal lubrication and can tolerate tough conditions. And they last longer than other sealing options, meaning you save in the long run.
Pro Tip: Inspect and look after your mechanical seals regularly for optimal performance and a longer lifespan.
Remember, if you keep your mechanical seals content, your pumps won't blow up! That's because no-one wants to deal with pump remains everywhere.
Installation and Maintenance Tips for Maximizing the Lifespan of Mechanical Seals
To maximize the lifespan of mechanical seals and ensure their efficient functioning, utilizing proper installation techniques is crucial. Routine inspection and maintenance procedures should also be followed to prevent potential issues. In case any problems arise, troubleshooting common issues with mechanical seals can help in resolving them effectively.Proper Installation Techniques and Considerations
Proper installation of mechanical seals is essential to maximize their lifespan. Incorrect installation can result in expensive repairs and downtime. Follow these simple steps for a successful installation:
- Preparation:
- Clean all components, check for dirt, debris, and damage.
- Ensure the seal dimensions fit the equipment specs.
- Use compatible lubricant or sealing compound.
- Alignment:
- Align the seal faces precisely.
- Use dial indicators or laser alignment devices.
- Check the shaft is aligned with the housing.
- Tightening:
- Tighten fasteners in a crisscross pattern.
- Follow manufacturer torque specs.
- Don't overtighten to prevent deformation.
Regular maintenance is also important to extend the lifespan of mechanical seals. Inspect them for signs of wear, leakage, or degradation and fix issues promptly. Additionally, lubricate them properly and ensure correct operating conditions (e.g., temperature, pressure).
Follow these tips to maximize your investment in mechanical seals. Proper installation minimizes stress, alignment ensures efficient operation, and appropriate tightening avoids damage. Maintenance addresses potential issues which enhances longevity. With these measures in place, you can prevent unexpected failures and downtime. Remember, neglecting maintenance is like letting a lover run wild without boundaries.
Routine Inspection and Maintenance Procedures
Regular inspections and maintenance are key to get the most out of mechanical seals. Here are some steps to follow:
- Check for leakage, corrosion, and wear. Look for cracks, vibrating, and misalignment.
- Clean the area around the seal. Remove dirt and any contaminants.
- Assess the lubrication system. Insufficient lubrication leads to friction and heat, which can damage the seals. Check all lubricant levels and consider replacements.
- Examine the seal material for deterioration or degradation from chemicals or temperatures. Replace any seals that are worn or don't meet specs.
- Verify that the bolts are secured tightly. Loose bolts cause misalignment and leaks.
- Conduct a test run of equipment with seals in place. Ensure proper functioning.
- Record observations, maintain a logbook, and follow manufacturer's or expert's advice.
Neglecting inspection and maintenance can result in a 60% reduction in mechanical seal life expectancy.
Troubleshooting Common Issues with Mechanical Seals
Mechanical seals can be prone to certain issues that can affect their performance and lifespan. Three common problems are:
- Leakage: Improper installation, wear and tear, or high operating temperatures can cause leakage. Regular inspection and maintenance can help spot and fix any leaks quickly.
- Excessive heat: Mechanical seals can generate a lot of heat during use. This can lead to seal failure, damaging the equipment. It is important to monitor temperature levels and ensure proper cooling.
- Contamination: Substances like dust, dirt, or chemicals can damage the performance of mechanical seals. Preventive measures should be taken to keep the environment clean.
Other factors can cause mechanical seal problems. For instance, misalignment between moving and stationary parts can be stressful for the seal faces, resulting in early failure. Adequate lubrication and replacing worn-out parts are also important for optimal performance.
A manufacturing plant had continuous breakdowns caused by seal failures in their pumps. Even with maintenance checks, the issue persisted. An experienced technician then found out that inadequate cooling water flow was causing too much heat in the seals. By adjusting the flow rate and better cooling, the problem was solved.
Mechanical seals are real-life superheroes, preventing leaks like caped crusaders!
Conclusion: The Significance of Mechanical Seals in Pump Systems.
Mechanical seals are key for pump systems. They keep leakage away and make sure operations run smoothly. There's no underestimating their importance!
Benefits of using them? Firstly, they keep liquids and gases in, preventing quality issues and potential hazards. Plus, they can handle extreme pressures, temperatures, abrasive liquids, and corrosive chemicals. This makes them ideal for industries like oil & gas, chemical processing, pharma, and water treatment.
Mechanical seals also make pumps more efficient. They reduce leakage and friction between moving parts - saving energy and money. With regular maintenance and inspection, as well as proper installation, seals will work optimally.
Lastly, get the right seal for the job! Think about pressure ratings, temperature limits, and fluid compatibility. This'll guarantee compatibility with system needs.
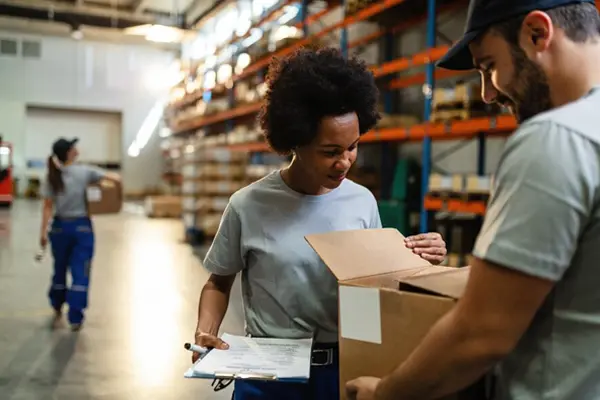
Request a quotation of your product
Looking for a specific product? Contact us and we will help you. We have a wide range of products and above all with excellent prices.