Siemens motors and their applications
What are the Different Types of Siemens Motors?
When it comes to industrial machinery, Siemens is a trusted name in the world of motors. But did you know that they offer a wide range of motors for various applications? In this section, we will dive into the different types of Siemens motors and their specific uses. From AC and DC motors to servo and stepper motors, we will uncover the unique features and benefits of each type. Whether you're looking for high torque or precise control, Siemens has a motor for every need.1. AC Motors
AC motors are a type of Siemens motor that is widely used in a variety of applications. When selecting an AC motor, it is important to take into account the following factors:
- Power requirements: Determine the necessary power for your specific application. AC motors are available in a range of power options to meet different needs.
- Speed control: Consider whether variable speed control or a fixed speed motor is needed. AC motors can be controlled using frequency inverters to adjust the speed as required.
- Efficiency: Look for AC motors with high energy efficiency ratings to reduce energy consumption and operating costs.
- Size and mounting: Consider the available space and mounting requirements for the motor to ensure proper installation.
- Protection features: Look for AC motors with built-in protection features such as overload protection and thermal protection to ensure safe and reliable operation.
By taking these factors into consideration, you can select the most suitable AC motor for your specific application.
DC motors - because sometimes you need a little direct current in your life.
2. DC Motors
DC motors are one of the many types of Siemens motors. They are commonly used in various industries and applications due to their unique characteristics. If you are considering DC motors, it is crucial to fully understand their features and functionalities. Here are some steps to take when exploring DC motors:
- Gain a basic understanding of DC motors, including their construction and operation.
- Consider the various types of DC motors available, such as brushed and brushless motors.
- Evaluate the power and torque requirements for your specific application.
- Take into account the control options available for DC motors, such as speed control and direction control.
- Consider the size, weight, and efficiency of the DC motor.
By following these steps, you can make an informed decision when selecting a DC motor for your application.
Servo motors - perfect for when you need precise control, and not so great for your budget.
3. Servo Motors
Servo motors, a type of Siemens motor, are widely utilized in various industries for their exceptional control capabilities. These motors operate based on feedback mechanisms that allow for precise positioning and speed control. When implementing servo motors, it is crucial to follow these steps:
- Determine the specific requirements of your application, including torque, speed, and accuracy.
- Select the appropriate model of servo motor based on these requirements.
- Ensure proper installation and connection of the motor.
- Configure and set up the motor's control system, including programming the desired motion profiles.
- Test and fine-tune the motor's performance to achieve the desired results.
Fact: Servo motors are commonly utilized in robotics, CNC machines, and automation systems due to their ability to provide precise and repeatable movements.
4. Stepper Motors
Stepper motors, specifically Siemens motors, are known for their ability to divide a full rotation into small, precise steps. They are commonly utilized in applications that require accurate positioning and control, such as 3D printers, CNC machines, and robotics. By converting digital pulses into mechanical motion, stepper motors allow for precise movement and positioning. They offer numerous benefits, including high torque at low speeds, exceptional positional accuracy, and the ability to hold their position even without power. Overall, stepper motors are a dependable and effective choice for applications that demand precise control and positioning.
In a factory that produces electronic devices, stepper motors are utilized in assembly robots to accurately position components during the manufacturing process. The use of stepper motors has greatly enhanced the precision and efficiency of the assembly line, resulting in higher-quality products and increased productivity. Thanks to the reliable performance of stepper motors, the factory has been able to meet the growing demand for their electronic devices while maintaining the highest standards of precision and quality.
From heavy machinery to robots, Siemens motors power it all; just make sure they don't gain sentience and take over the world.
What are the Applications of Siemens Motors?
With their advanced technology and high-performance capabilities, Siemens motors have become a popular choice in a wide range of industries. In this section, we will explore the various applications of Siemens motors and their impact in different areas. From powering industrial machinery and vehicles to being used in the aerospace and robotics industries, we will delve into the versatility and efficiency of Siemens motors. Join us as we take a closer look at the applications of these powerful motors.1. Industrial Machinery
Industrial machinery plays a crucial role in various sectors, and Siemens motors are widely utilized in this field due to their reliability and performance. When it comes to incorporating Siemens motors into industrial machinery, it is important to follow these essential steps:
- Identify the specific requirements of the machinery and determine the appropriate type of Siemens motor.
- Ensure proper installation of the motor, adhering to manufacturer guidelines and industry standards.
- Regularly inspect and maintain the motor to prevent any potential issues and ensure optimal performance.
- Monitor the motor's performance and efficiency to identify any deviations or abnormalities.
Pro-tip: For guidance on selecting, installing, and maintaining Siemens motors in industrial machinery, it is recommended to consult with Siemens experts or authorized technicians. Their expertise can help maximize the efficiency and lifespan of the motors, reducing downtime and improving overall productivity.
Siemens motors make cars run smoothly, just don't forget to buckle up.
2. Automotive Industry
Siemens motors have played a crucial role in the automotive industry for many years, powering various applications such as electric power steering, HVAC systems, and electric vehicle propulsion systems. These motors offer numerous advantages, including high efficiency, high torque, precise control, and a long lifespan. Proper installation, maintenance, and regular inspections are necessary for safety, and it is also important to follow the manufacturer's guidelines.
3. Aerospace Industry
The aerospace industry relies on Siemens motors for various applications such as aircraft propulsion, landing gear systems, and cabin equipment. When using Siemens motors in the aerospace industry, it's important to follow safety measures to ensure optimal performance and prevent accidents. Here are some steps to consider:
- Properly install and maintain the motors to ensure they function correctly.
- Follow the manufacturer's guidelines for operating and handling the motors.
- Regularly inspect and repair the motors to identify any potential issues.
Fact: Siemens motors are specifically designed to meet the stringent requirements of the aerospace industry, providing reliable and efficient performance in demanding environments.
Robots may take over the world one day, but until then, let's use Siemens motors to power them.
4. Robotics
Siemens motors play a crucial role in the field of robotics, powering the movement and functionality of robotic systems. These motors offer several advantages that make them highly suitable for robotics applications.
- High Efficiency: Siemens motors are designed to operate with high efficiency, minimizing energy consumption and maximizing the overall performance of the robotic system.
- High Torque: These motors provide high torque output, enabling robots to exert sufficient force to perform tasks accurately and efficiently.
- Precise Control: Siemens motors offer precise control over speed, position, and acceleration, allowing robots to execute complex movements with accuracy and repeatability.
- Long Lifespan: With their robust design and high-quality construction, Siemens motors have a long lifespan, ensuring reliable operation in demanding robotic environments.
What are the Advantages of Using Siemens Motors?
When it comes to industrial motors, Siemens is a well-known and trusted brand. Their motors have been used in a wide range of applications, from manufacturing plants to transportation systems. But what sets Siemens motors apart from others? In this section, we will delve into the advantages of using Siemens motors, including their high efficiency, powerful torque, precise control, and long lifespan. Each of these features plays a crucial role in the performance and reliability of Siemens motors, making them a top choice for many industries.1. High Efficiency
High efficiency is a key advantage of utilizing Siemens motors. To ensure maximum efficiency in motor operation, follow these steps:
- Choose the appropriate motor size for your application to avoid overloading.
- Ensure proper installation and alignment to minimize energy losses.
- Implement efficient cooling and ventilation systems to prevent overheating.
- Utilize variable speed drives to optimize motor speed and reduce energy consumption.
- Regularly maintain and inspect motors to identify and resolve any efficiency issues.
By following these steps, you can maximize the efficiency of Siemens motors and achieve significant energy savings. Incorporating high-efficiency motors in your operations is not only environmentally friendly but also helps reduce operating costs and improve overall system performance.
With high torque, Siemens motors can handle any job with ease - unless you're asking them to do your laundry, then you're on your own.
2. High Torque
High torque is a key advantage of Siemens motors, making them suitable for applications requiring powerful rotational force. Here are some steps to consider when utilizing Siemens motors with high torque:
- Select the appropriate Siemens motor model that offers high torque capabilities.
- Ensure that the motor is properly sized and matched to the load requirements.
- Implement a robust control system that can effectively manage and utilize the high torque output of the motor.
- Perform regular maintenance and inspections to keep the motor operating at its optimal performance and prevent any potential issues.
By following these steps, you can maximize the benefits of high torque offered by Siemens motors in your applications. Remember to always consult the manufacturer's guidelines and seek professional assistance when needed.
With Siemens motors, you'll have more precision than a surgeon's scalpel in your industrial machinery, automotive vehicles, aerospace equipment, and even your robotic minions.
3. Precise Control
Precise control is a key advantage of using Siemens motors, ensuring accuracy and efficiency in various applications. To achieve precise control with Siemens motors, follow these steps:
- Calibration: Properly calibrate the motor to ensure accurate positioning and movement.
- Tuning: Adjust the motor's parameters to achieve the desired speed, torque, and acceleration.
- Feedback: Utilize feedback devices like encoders to provide real-time information on the motor's position and speed.
- Control algorithms: Implement advanced control algorithms to regulate the motor's performance and response.
Pro-tip: Regularly monitor and fine-tune the control parameters to maintain optimal performance and precision in Siemens motors.
Unlike overly dramatic reality TV stars, Siemens motors have a long lifespan and won't leave you disappointed after just one season.
4. Long Lifespan
Siemens motors have gained a reputation for their exceptional longevity, thanks to their high-quality construction and durability. To ensure that your Siemens motor lasts for a long time, follow these steps:
- Proper maintenance: Regularly inspect and clean the motor to prevent the buildup of dirt and debris.
- Temperature control: Operate the motor within its specified temperature range to avoid overheating and premature failure.
- Load management: Avoid overloading the motor beyond its rated capacity to prevent excessive wear and tear.
- Lubrication: Use recommended lubricants and follow the manufacturer's guidelines for proper lubrication intervals.
Siemens has been manufacturing motors for over 150 years, constantly innovating to enhance their performance and lifespan. With a strong commitment to quality and reliability, Siemens motors have become a trusted choice in various industries worldwide.
What are the Safety Measures for Using Siemens Motors?
When it comes to using Siemens motors, safety should always be a top priority. These high-performance motors are used in a wide range of industrial applications, and improper use can lead to serious accidents and costly damages. In this section, we will discuss the essential safety measures for using Siemens motors. From proper installation and maintenance to following the manufacturer's guidelines, we will cover everything you need to know to ensure the safe and efficient operation of these powerful motors. Let's dive in and learn how to use Siemens motors safely.1. Proper Installation and Maintenance
For optimal performance and longevity of Siemens motors, proper installation and maintenance are crucial.
- Installation: Follow these steps for proper installation:
- Ensure the motor is compatible with the application requirements.
- Use appropriate mounting techniques to prevent vibrations.
- Securely connect electrical connections according to the manufacturer's guidelines.
- Perform a thorough inspection of the motor before installation.
- Verify proper alignment between the motor and driven equipment.
- Maintenance: Implement these practices for effective maintenance:
- Regularly inspect the motor for any signs of wear or damage.
- Clean the motor to remove dust and debris that could affect performance.
- Ensure proper lubrication of bearings and other moving parts.
- Check and tighten electrical connections to prevent loose connections.
- Follow the manufacturer's recommended maintenance schedule.
2. Following Manufacturer's Guidelines
- Read the user manual thoroughly to understand and follow the specific guidelines provided by the manufacturer.
- Adhere to the recommended operating conditions, including voltage, current, and temperature limits.
- Ensure proper installation according to the manufacturer's instructions, including correct wiring, grounding, and mounting.
- Regularly inspect the motor for any signs of wear, damage, or overheating.
- Perform routine maintenance tasks outlined in the manual, such as lubrication, cleaning, and adjustment.
- Use only approved accessories and replacement parts provided by the manufacturer.
- Avoid overloading the motor by not exceeding the recommended load capacity.
- Keep the motor in a clean and dry environment, away from moisture, dust, and corrosive substances.
- Immediately report any irregularities, malfunctions, or safety concerns to the manufacturer.
3. Regular Inspections and Repairs
Regular inspections and repairs are essential for maintaining the performance and longevity of Siemens motors.
- Visual Inspection: It is crucial to regularly examine the motor for any signs of damage, such as loose connections, frayed wires, or overheating.
- Cleaning: Keep the motor clean by removing dust, debris, and other contaminants that may hinder its operation.
- Lubrication: Proper lubrication of the motor's moving parts is necessary to prevent excessive wear and tear. Follow the manufacturer's guidelines for best results.
- Testing: Periodic tests should be conducted to check the motor's functionality, including voltage, current, and speed measurements.
- Repair or Replacement: If any issues are detected during inspections or testing, it is important to promptly address them by repairing or replacing the faulty components.
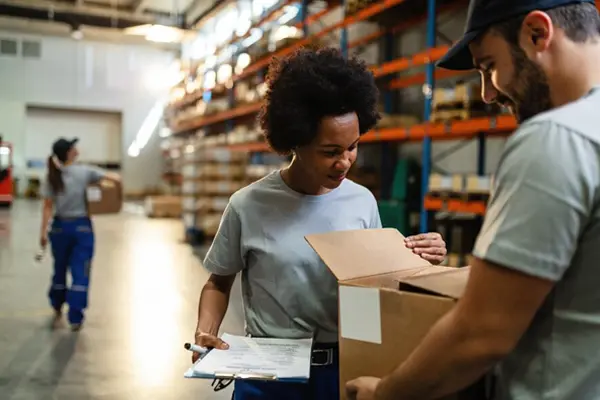
Request a quotation of your product
Looking for a specific product? Contact us and we will help you. We have a wide range of products and above all with excellent prices.